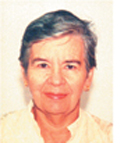
Ma. Isabel Ongpin
JUST back from a week in India to check out a small feature of their textile industry. India is a huge country with a huge population and is a subcontinent shared with Pakistan and Bangladesh.
Already have an active account? Log in here.
Continue reading with one of these options:
Continue reading with one of these options:
Premium + Digital Edition
Ad-free access
P 80 per month
(billed annually at P 960)
- Unlimited ad-free access to website articles
- Limited offer: Subscribe today and get digital edition access for free (accessible with up to 3 devices)
TRY FREE FOR 14 DAYS
See details
See details
If you have an active account, log in
here
.